No one wants to fly on a plane where manufacturers and engineers cut corners. Precision isn’t just a goal, it’s a necessity for aerospace parts manufacturing. As an aerospace engineer, the consequences of a flawed part can range from reduced fuel efficiency to catastrophic system failure. But when it comes to translating designs into finished components on the shop floor, what are the most critical production factors to watch? Buckle your seatbelt and return your seats and tray tables to their original positions. Below are four key machine shop production tips that every aerospace engineer should know during aerospace part development and collaboration with machining partners.
Aerospace Parts Manufacturing Essentials
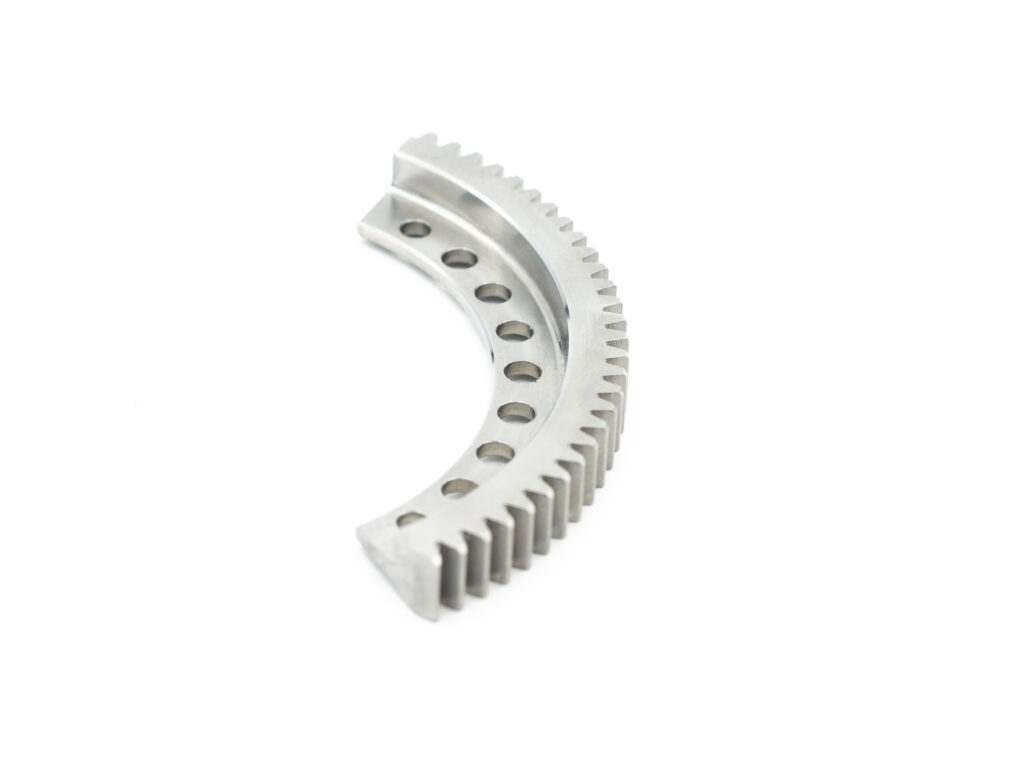
1. Tight Tolerances and Repeatability Are Non-Negotiable
Aerospace parts often operate under extreme stress, temperature variation, and vibration. That means tolerances as tight as ±0.0001” aren’t just desirable—they’re required. But achieving this level of precision consistently across dozens or hundreds of parts takes more than capable machines.
Your machining partner must use CNC equipment with thermal stability, in-process probing systems, and precision workholding to reduce variation. Look for shops that use statistical process control (SPC) to monitor outputs and minimize drift.
As an engineer, collaborate early with manufacturing teams to understand what tolerances are critical and where you might build in some flexibility—especially for non-functional or secondary features. This can reduce manufacturing time and cost while maintaining mission-critical performance.
2. Know the Nuances of Aerospace Parts Materials
The aerospace industry demands high-performance materials like titanium alloys, Inconel, Hastelloy, and carbon composites for their strength-to-weight ratios and resistance to heat and corrosion. These materials are great in the air—but can be tough on tools and equipment.
For instance:
- Titanium tends to retain heat, which leads to rapid tool wear unless properly cooled.
- Inconel work-hardens quickly, requiring light cuts and rigid setups.
- Carbon fiber composites demand dust control and special cutters to prevent delamination.
From a design standpoint, recognize the machining challenges that your material selection can create. Where possible, specify standardized alloys or engineer around known machining issues. A slight design tweak can significantly reduce tool wear, cycle time, and scrap rate.
3. Build Quality Assurance Into the Process, Not Just the End
In aerospace, quality control isn’t just about inspecting finished parts—it’s about designing quality into every step. If your part requires airworthiness certification, traceability, and material validation, your manufacturing partner must follow rigorous protocols like AS9100 compliance. The FAA requires certifications from parts manufacturers to assure airworthiness.
Make sure designs include:
- Clear GD&T callouts for CMM inspections
- Defined surface finish requirements
- Material certificates and process specs (e.g., heat treating, anodizing, NDT)
Also, get involved early in the discussion about measuring strategies. Some internal geometries or features may be difficult to inspect non-destructively, and this can influence design or tolerancing decisions.
4. Cleanliness Isn’t Just Cosmetic—It’s Safety-Critical
Foreign Object Debris (FOD) in aerospace machining isn’t just a nuisance; it’s a potential hazard. A loose sliver of metal, a fingerprint, or a spec of composite dust can lead to in-flight component failure or downstream contamination in sensitive assemblies.
As an engineer, consider designing parts with FOD control in mind. Avoid features that are nearly impossible to clean or inspect, and specify protective packaging or handling procedures for critical surfaces.
Make sure your machining partner maintains:
- FOD-controlled zones or clean rooms
- Segregated tooling and fixturing for aerospace-only production
- Air filtration and chip management in carbon composite or exotic metal areas
Cleanliness also affects coatings and bonding. Even a lightly contaminated surface can cause adhesive failures or irregular anodizing results. Proper handling protocols are part of manufacturing integrity—especially in aerospace.
The Final Approach
Aerospace parts machining is a high-stakes game, where precision, material science, inspection, and cleanliness all converge. As an aerospace engineer, the more you understand the practical realities of part production, the better positioned you’ll be to design parts that are not only functional but manufacturable and certifiable. The right manufacturing partner will help highly engineered parts touchdown safely when produced, assembled and integrated safely into any aircraft.