CNC Swiss Screw Machining
About Swiss Machining
Swiss machining or CNC screw machining involves an automatic lathe that has a sliding headstock and a guide bushing. The sliding headstock secures the bar stock, rotates it, and moves it forward to create the required lengths, while the cutting tools move in and out of the material to create specified diameters. The headstock contains the collet, which clamps the material. The material is then fed through a guide bushing, which is usually made of carbide. The bushing is adjusted so that the material can slide through it, but tight enough to keep the material from flexing away from the cutting tool. The guide bushing allows Swiss-type screw machines to hold very tight tolerances (+/-.0001″) over long lengths in relation to part diameter. For example, if you needed to turn a .100″ diameter over a 3″ length, a Swiss-type screw machine is the only way to do this. On a conventional lathe the material would bend away from the cutting tool.
In Swiss machining the workpiece can be transferred between main and back spindles, enabling machining of both ends of a part.
As a result, the machines are able to produce small, intricate parts complete in one chucking. CNC screw machining addresses two hot issues in manufacturing: The need to produce parts for increasingly miniaturized devices, and the quest to reduce costs by eliminating secondary operations and minimizing part-handling time.
Equipped to Meet Your Swiss Screw Machining Needs
Nolte meets your Swiss screw machining needs with industry-leading CNC Swiss machining equipment that produces custom precision machined components from low to high volume and complexity to your specifications. Our CNC Swiss equipment allows us to manufacturing tight tolerance components with difficult geometric designs in one operation and length to diameter ratios. Our equipment is capable of optimally machining diameters from 8 to 38mm and lengths up to 250mm.
CNC Swiss Screw Machining FAQ
Swiss screw machining was originally developed to produce small, complex parts for watches. CNC Swiss screw machines employ a sliding headstock that feeds a rotating workpiece through a collet and bushing. Static and rotating side-and end-working tools cut the part as it is fed. The workpiece can be transferred between main and back spindles, enabling machining of both ends of a part.
- Turning
- Drilling
- Boring
- Milling
- Threading
- Tap
- Reaming
- Polygon Turning
- Gear Hobbing
- Thread Milling
- Flat Milling
- Key-way Milling
- Cross Drilling
- Cross Tapping
- Broach
- Knurling
- Engraving
- Burnishing
- Laser Engraving
- Wire EDM
- Grinding
- Thread Rolling
- Assembly
- Special Packaging
- Steels – Alloy, Carbon, Stainless
- Non-Ferrous – Aluminum, Brass
- Zinc
- Plastics
- Cast and Sintered Metals
- Forgings
We work with tolerances of .0005″
Diameter size ranges from 8 – 38 mm, with a maximum length of 20″.
We can take care of heat treating, anodizing, plating, painting, and welding services. Make Nolte your one-stop job shop!
We do offer laser engraving and dot peen part marking services.
Advantages You Enjoy with Nolte
- Experienced Precision Machining Expertise
- Just In Time Delivery of Parts
- AS9100 Rev. D Including ISO 9001:2015
- Flexible Order Volume for Changing Markets
- Expert Cost Assessment
- Volume Material Purchasing
- Light Assembly Services
“When Nolte says they’re going to do something, they do it. It’s nice to work with a company that you feel has a lot of integrity.”
-Sandy E.
-Senior Buyer at BAE Systems (Military Contractors)
Fairfield, OH
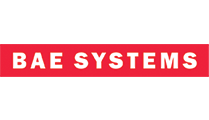
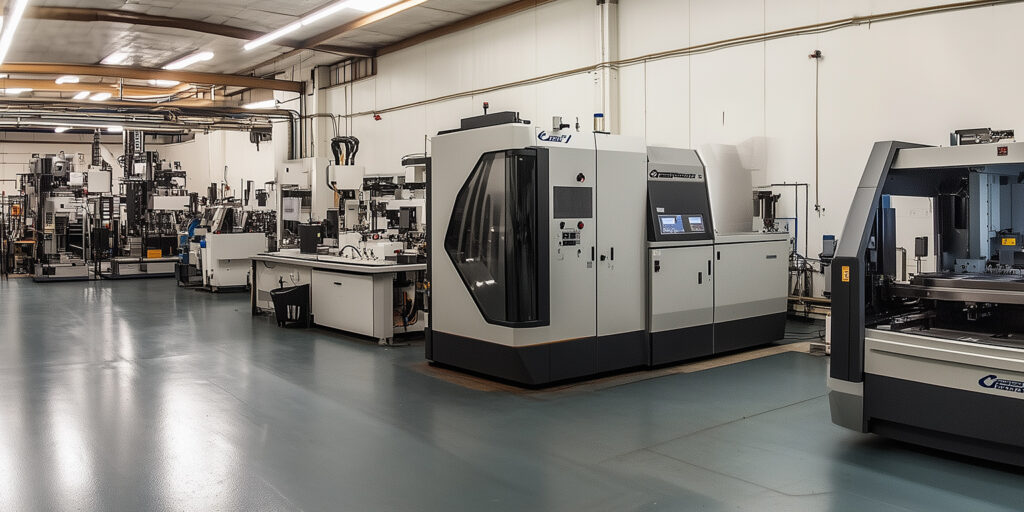
Your Partner for Higher Efficiency and Lower Total Costs
As your swiss screw machine shop, the Nolte team does more than supply you with your parts made to specification and delivered on time. We consider those to be normal expectations of doing business. Our goal is to surpass expectations by helping you discover better, more cost-efficient ways to manufacture your parts. Meeting your current and future needs through flexibility and responsiveness is another commitment we make to you. As a regional top-notch swiss screw machining job shop, you can count on our team as an extension of your our team, ready, capable, and dedicated to your success.
Dependable Quality and Consistency
Use of the industry’s leading CAD/CAM software allows us to verify machining processes prior to launch on the production floor. Our Swiss Machining equipment delivers rapid, consistent and programmable control, for a design that is easily manufactured with the highest levels of quality and consistency.
Contact us for an appointment to begin the Nolte Precise Process and discover a total cost solution to CNC screw machining and parts fulfillment needs.