Value Added Advantage for Defense Client
Engineering Reviews are another Value Added Advantage for Nolte Precise defense client
Background
A multinational defense contractor used a weldment assembly to attach armor plating to military vehicles. The performance of the weldment assembly was critical in the installation of armor plate and protecting our soldiers in theater.
Problem
The defense contractor needed to identify areas to reduce total costs of their armor plating process. Due to the volume of the weldment assemblies used, this component offered an opportunity to identify meaningful costs savings. However, the current design was tried & true and performed well over the vehicles life. The defense contractor had major concerns in changing anything that had to do with protecting service members. Any improvement needed to reduce costs and in absolutely no way reduce human safety.
With that in mind, Nolte Precise engineering went to work.
Opportunity for Improvement
Nolte Precise engineering went to work and identified several areas of opportunity for improvement. Nolte engineers noted that the manufacturing costs for the machined insert were very expensive and the installation was cumbersome. Nolte engineering assisted customer design engineers to develop an insert that could be produced and installed more efficiently. Nolte manufactured sample parts and provided to the customer.
Result
After initial testing, the re-designed inserts not only proved to effectively reduce the total cost of the assembly, but they performed better in torque testing over the initial design.
After completing the necessary process verification steps, the re-design was implemented by the customer. Not including the performance gains of the weldment assembly, the component cost savings amounted to 58% of the original cost and resulted in recurring annual savings exceeding $1 million.
Contact us for an appointment to begin the Nolte Precise Process and discover a total cost solution to your defense industry machined parts fulfillment requirements.
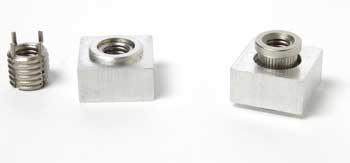
“Nolte is in the top 5 of our 75 suppliers, in working with us to make the most of our lean and inventory management
processes.”
Karen K., Supply Chain Manager at Parker-Hannifin’s Oildyne Division (Diversified Manufacturing Company), Minneapolis, MN
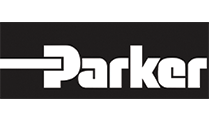